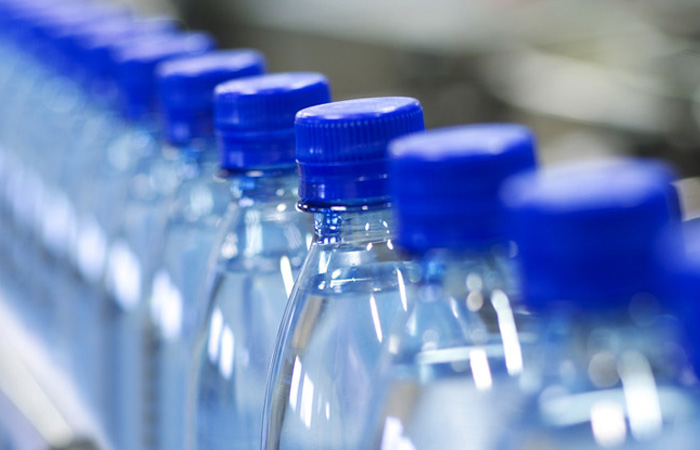
Structure and working principle of automatic Blow Molding Machine
1. The main structure and principle of the machine
1.1, clamping part
The positioning rack is balanced and positioned, the front, middle and rear three templates, the double crank arm linkage mechanism, and the mold clamping cylinder. The cylinder is driven by the electromagnetic directional control valve to drive the crank arm to open and close the mold. The structure is reasonable in design, stable in operation and large in clamping force.
1.2, stretch the blowing part
It is composed of a stretch solenoid valve, a high-pressure blowing valve, a pull-body sealing cylinder, a movable sealing seat, and a blowing air reservoir. When working, the piston of the stretching cylinder is pushed through the directional control valve to drive the stretching rod and the sealing cylinder to push up on the preform that has been closed. The sealing cylinder seals the mouth of the preform, and the stretching rod is heated and elastic to the preform. At the same time, the gas stored in the gas storage cylinder is stretched longitudinally, and the preform is bottom blown by the high-pressure blowing valve through the sealing cylinder, and then the preform is subjected to high-pressure inflation molding.
1.3. The heating chain plate passes through the first station of the stepping cylinder, is detected and positioned by the photoelectric switch, and then blown into the product by the molding mechanism. The stepping cylinder is pushing a station to detect and position, and continuous production is repeated.
1.44. The self-rotating chain is driven by the motor to work continuously, so that the preform in the drying tunnel is heated quickly and evenly.
1.5. The preform is conveyed and sorted through the feeding system, and the preform is installed on the bottle blowing machine base by the conveying manipulator and enters the drying tunnel
1.6. The heating consists of two relatively independent far-infrared lamp ovens. Each far-infrared lamp of each oven can be adjusted longitudinally according to different preforms.
1.7. Preform heating. While the preform rotates to make it evenly heated, the bottle mouth is cooled, and then hot air is blown to the preform by a fan to make the inner and outer walls of the preform evenly heated.
1.8. After the preform enters the blowing mold, the pre-blowing air enters to stretch the blown preform in the ring direction; when the stretching rod reaches the bottom of the mold, high-pressure air enters the cavity to further stretch the preform, making the bottle wall tight Paste mold bi.
1.9. The high pressure gas is kept in the mold for a certain period of time, on the one hand, it eliminates the internal pressure caused by the stretching of the preform.
On the other hand, make the bottle wall close to the mold wall to improve the crystallinity of the bottle plastic.
1.10. After the high-pressure gas is over, the venting and demolding will begin.
1.11, the blowing process is over.
1.12. The bottle is conveyed to the bottle-loading station through the chain plate, which is picked up by the bottle-loading cylinder, and then blown out by the airflow.
2. Blowing process adjustment
2.1. Installation and operation (notes)
1. Promote standardized operation actions;
2. When blowing the thermos bottle, pay attention to the damage to the body caused by the high temperature of hot kerosene. The mould is 125℃-135℃, and the mould temperature machine is 140℃-150℃.
3. Please turn off the control power when testing the mold temperature;
4. Pay attention to the damage to the body when the high pressure gas joint is loosened;
2.2. Blow molding conditions
1. Temperature: including:
A. Setting of lamp power;
B. The temperature setting of the exhaust fan;
C. The influence of ambient temperature on the heating box
D. The temperature of the hot mold: 125°C—135°C, water bottle mold 10—15°C;
2. Pressure: including:
A. Pre-blowing pressure is 5-15 kg/cm², the actual pressure is 9-12 kg/cm²;
B. Bottle blowing pressure: cold bottle 25-30 kg/cm²;
C. Cyclic blowing: 15 kg/cm²;
3. Flow rate: the speed when the pre-blowing pressure is constant.
4. The speed of the tie rod: The speed at which the tie rod rises is directly related to the stretching of the preform.
5. Forming settings:
A. Pre-blowing delay.
B. Blowing delay.
C. Blow time, exhaust time, etc.
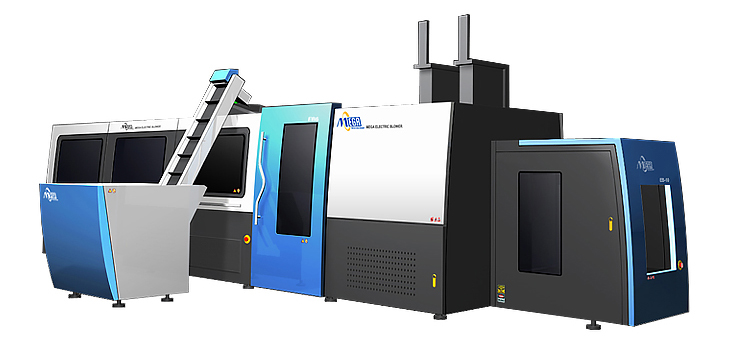